Enhancing Efficiency and Sustainability
The coal mining industry faces a range of challenges as it strives to improve equipment reliability, increase productivity, and reduce costs.
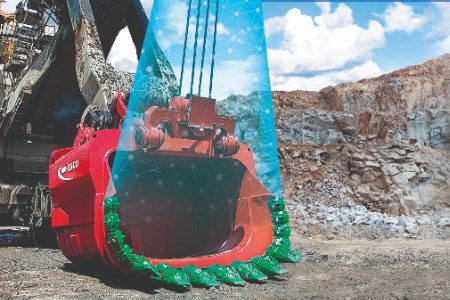
Amid a global push for sustainability and the United Nations’ Sustainable Development Goals (SDGs), coal producers are under pressure to address energy usage and carbon dioxide (CO2) reduction.
Recognizing coal’s ongoing significance in global energy base load, this article explores how Weir ESCO’s tailored approach, technological advancements, and innovation in the cable shovel space play a pivotal role in assisting coal producers in addressing these challenges.
Addressing current coal mining challenges
The coal mining industry is grappling with the age-old pursuit of enhancing equipment reliability and productivity while managing costs. Environment, social, and corporate governance (ESG) principles, which have been a part of the industry for decades, now intertwine with the renewed global focus on sustainability, prompting a deeper emphasis on improving equipment performance and creating greater efficiencies that save energy while reducing CO2 emissions. In the face of global efforts to transition to renewable energy sources, coal continues to play a vital role as a power source, necessitating coal producers to implement environmentally conscious practices by choosing equipment, attachments, and wear parts that reduce waste and improve the performance of their operations.
Cable shovel efficiency: Room to innovate
Cable shovel efficiency improvements have remained a challenge due to the complexity of influencing pass matching on what is the most efficient truck-loading machine in a mine. Over the past two decades, the introduction of lightweight truck trays has presented an opportunity for incremental dipper performance improvements, aligning with the enhanced payload capabilities. In certain scenarios, a reduction in the number of passes required to fill a truck can be achieved, leading to optimised shovel and truck productivity. This progression in dipper performance optimisation, synchronised with evolving truck design, underscores the potential for innovation in enhancing cable shovel efficiency.
A compelling case study showcases Weir ESCO’s role in optimising pass matching outcomes. In a coal mine in North America, the integration of an optimised dipper design coupled with the Nemisys® N1 lip and GET system resulted in a reduction from five passes to four for the client’s P&H 2800 class machine. This example highlights the practical application of innovative solutions within mining operations that bring significant sustainable improvements for the mine operator.
Save to read list